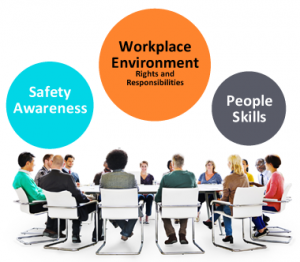
Toolbox Tailgate Meetings
Toolbox meetings (tailgate meetings or crew talks) can be an effective way to deliver information, introduce new concepts, skills or procedures, and generate work-based discussions. Although most prevalent in the construction industry, toolbox meetings can be used to promote safety in the spectrum of workplace industries, environments and situations. Seizing the opportunity to hold an informal meeting in the lunch room, site trailer – or even in the parking lot after work – can result in the chance to refresh and review training, or introduce and discuss new equipment, procedures, etc.
Any workplace meeting, no matter how informal, should be conducted by a facilitator –usually qualified and competent member of the management or supervisory team who is confident in leading, motivating and teaching employees in a non-biased manner. If the meeting provides a comfortable, informal setting for all participants to voice any issues or concerns or offer insight into the daily operations of the company, toolbox meetings can be an very effective forum for discussing the current state of affairs in the workplace,. Allowing an open forum for discussing workplace issues fosters a sense of inclusion for all crew members, and will perhaps result in a greater commitment to increased productivity and success.
When establishing an agenda for a toolbox meeting, first establish a strong and specific focus that will retain the attention of meeting attendees – keeping in mind that shorter meetings tend to yield more effective results. As well, provide attendees with an opportunity to take something away from the meeting – be it a newly acquired skill, useful information that will allow them to perform their jobs better, or even just the sense that they are actively involved in the operation of the company.
At the onset of the meeting, the meeting facilitator should clearly establish the topic that will be focused on, and the expected outcomes of the meeting; for example, the facilitator may begin the meeting by saying, “Today, we’re going to discuss the new shop sander. At the end of this meeting, I want you to understand how to operate it safely, and what PPE is required when you use the sander.” By providing a specific focus for the meeting, attendees know what to expect and will be prepared to take in the information.
In order to retain the attention of meeting attendees, the facilitator must find some common ground amongst all attendees; in particular, close consideration must be given to such things as the language, topic and length of the discussion. Think of potential cultural barriers such as language when developing your topic material, as some of the attendees may be new to English. As well, use widely-accepted terminology that all workers (at all skill levels) can easily understand, and keep the meeting (relatively) short, to-the-point, and focused on the topic-at-hand.
Another key element to conducting a successful toolbox meeting is establishing an open and accepting forum for all attendees. At the onset of a meeting, the facilitator should make it clear that if anyone has issues or questions, they can confidentially ask for assistance. During the meeting, the facilitator should be also aware of the crew’s needs, communication issues and potential learning issues, and be sure to assess whether they need to speak with an employee in private to ensure that the desired understanding has been achieved.
Meeting facilitators should keep meeting minutes to note the time, date and attendance of the meeting, along with the topic in focus and any relevant notes that are generic enough to be understood by other personnel who may wish to review the meeting minutes.
During the meeting process, the facilitator should encourage active participation from all attendees by staging brainstorming sessions or providing them with a hands-on opportunity to practically apply a new skill. Using open-ended questions is an effective way to generate round-table discussions, just be sure to enforce an open, honest and accepting environment in which all attendees will be able to express themselves freely.
Toolbox meetings are often most effective when the facilitator does not dominate the meeting with some long, drawn-out oral presentation. Implementing teaching aids such as videos, demonstrations, slides, and various props can relieve the monotony of a lecture-type presentation, and better retain the attention of attendees.
Allowing attendees to learn about new equipment and/or procedures and have the opportunity to exercise practical application of any new skills can also be an extremely effective method for conducting toolbox meetings. Meeting facilitators should adhere to the ‘See, Hear, Do’ method of instruction, in which they demonstrate and explain something (for example, a new skill or procedure), then have attendees apply the new information in a hands-on way. That way, the leader gets the chance to confirm that all attendees understand the topic-at-hand, get feedback and field questions from attendees.
Establishing and maintaining a sense of positivity is perhaps the most important aspect to toolbox meetings (and life in general). Meeting facilitators must strive to keep the topic interesting, keep employees actively involved in the process, and foster a strong, successful learning environment. Every attendee should have equal access to the information at hand, equal abilities to master their understanding of any techniques or procedures that have been demonstrated, and equal opportunity to apply any new skills or concepts within the presence of (and therefore, with the feedback of) the meeting facilitator.
As in any learning situation, it is critical to the success of toolbox meetings that the employees’ understanding, knowledge and/or skills are reinforced, assessed and re-examined. The best results can be achieved by providing feedback (both positive and negative, where necessary), supervision and correcting any mistakes before the worker applies the knowledge/skill in an actual rather than staged setting. Seize the opportunity to conduct toolbox meetings whenever necessary – after all, an effective toolbox meeting can (at times) mean life or death when it comes to workplace safety.